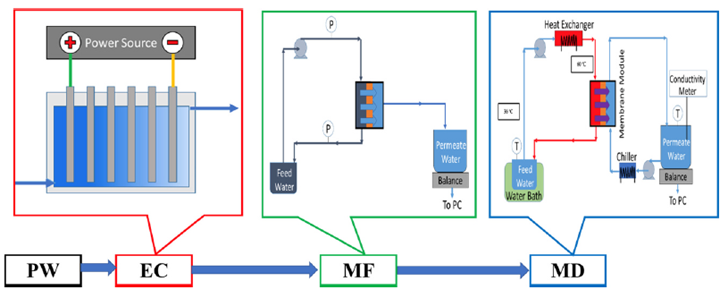
Fig. 1 Scheme of Research
INTRODUCTION
Water that is co-produced during oil and gas production, known as produced water (PW), is a major waste stream. The United States produces about 21 billion barrels of PW per year. The amount of PW that is generated depends on the geological formation and the type of energy resource being developed. Here we focus on hydraulic fracturing and horizontal drilling, which have enabled the recovery of oil and gas from shale and other tight rock formations. However, this technology requires the use of a large amount of water.
Treating hydraulic fracturing flow back and co-produced water, referred to here collectively as PW is very challenging and expensive. Fracking fluid is pumped into the well at high pressure in order to fracture the rock formation. The fracking fluid consists of 98% water and sand. However, a number of chemicals such as friction reducers, surfactants, corrosion inhibitors and flow improvers are added. After fracturing the rock formation, the pressure is reduced, and the fracking water flows back to the surface with oil/gas and co-produced water.
The composition of the PW water depends on the geological formation where it is trapped. In general, the PW contains high concentrations of dissolved salts referred to as total dissolved solids (TDS). In addition, there are dissolved polar and nonpolar organic compounds (total organic carbon, TOC) and oil, grease, fuels, and additives associated with the fracking fluids that make up the total suspended solids (TSS).
MATERIALS AND METHOD
A. PW Characterization
PW was obtained from a hydraulic fracturing facility in Texas, USA. Prior to testing, the water was analyzed at the Arkansas Water Resources Center, University of Arkansas (Fayetteville, AR, USA). Total dissolved solids (TDS), total suspended solids (TSS), turbidity and total organic carbon (TOC) were measured using EPA standard methods 160.1, 160.2, 415.1 and 180.1, respectively. Cations and anions were measured using EPA methods 200.7 and 300.0, respectively. Conductivity was measured using a conductivity meter.
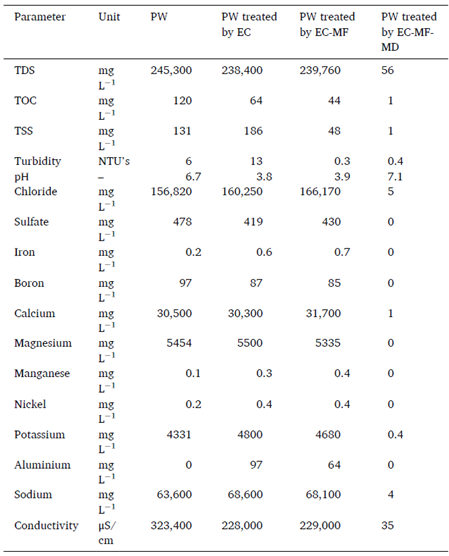
B. Electro Coagulation and Micro Filtration Pretreatment
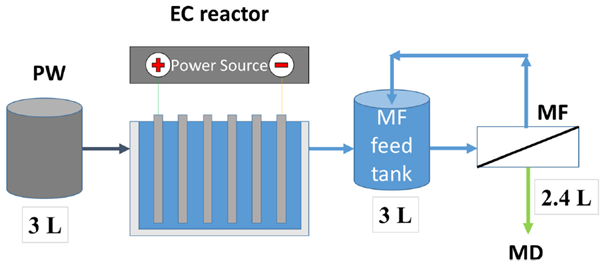
A diagram of the combined EC-MF system is shown in Figure. A custom-built polycarbonate reactor having dimensions of 4 cm × 32 cm × 40 cm with a total volume of 5120 cm3 was used to conduct all the EC experiments. Six aluminium electrodes were fitted vertically inside the reactor with a 5 mm inter-electrode spacing and a total effective surface area of 3760 cm2. A DC power supply (Hewlett Packard, Palo Alto, CA, USA) was connected to a reverse polarity switch which enabled the direction of the current to alternate every 30 s. This is essential to prevent the formation of a passivation layer on the electrode, which would suppress further reactions.
Immediately after EC, microfiltration was conducted using a custom-built MF cell developed in previous work. The entire 3 L of EC treated feed water was placed in the MF feed tank. Initially, the permeate outlet was closed, and feed was recirculated through the membrane module by means of a diaphragm pump (P800, King-Kong, Taiwan). The membrane surface area available for filtration was 33.75 cm2. The feed flow rate was 1.8 L/min, and the feed pressure was 110 kPa. The permeate side pressure was essentially at atmospheric pressure. Once a steady-state had been reached, the permeate outlet was opened and permeated was collected in the permeate tank, which was placed on a computer-connected analytical balance (Mettler Toledo, Columbus, OH). The permeate flux was calculated based on the rate of permeate collection in the permeate tank. About 80% of the EC treated water was recovered. After each cycle, the membrane was cleaned by circulating DI water for one hour prior to starting a new cycle. A commercially available PES membrane purchased from Membrane Science Inc. (Hsinchu, Taiwan) and having a porosity of 80.4%, 0.1 μm pore size and 43.7o air contact angle was used.
C. Membrane Distillation
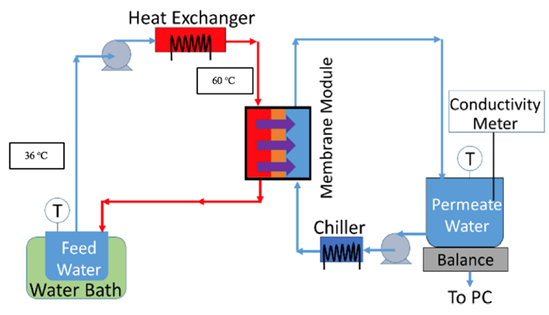
Fig. 3 Scheme of MD
A diagram of the MD system is shown. A custom-made acrylic membrane cell with a 40 cm2 effective membrane area and 2 mm deep channels were used as the membrane module. PTFE spacers (ET 8700, Industrial Netting, Minneapolis, MN, USA) were used for mechanical support and mixing. Feed and permeate streams were pumped on opposite sides of the membrane at 0.05 L/min using two peristaltic pumps (Masterflex I/P, Cole Parmer, Vernon Hills, IL) in counter-current flow. The weight of the permeate was measured and recorded by a computer-connected analytical balance (Mettler Toledo, Columbus, OH, USA). The temperature of the permeate tank was maintained at 20 ◦C using an external chiller (PolyScience, Niles, IL, USA). The feed tank was placed in a water bath to maintain the temperature at 36 ◦C. The feed water was pumped through a heat exchanger in order to increase the temperature of the feed entering the MD module to 60 ◦C. From our previous work, we found that cooling the feed tank relative to the temperature of the feed entering the MD module induces precipitation in the feed tank and suppresses scale formation on the membrane surface due to supersaturation of the feed. In this way, we increase water recovery and limit scale formation on the membrane surface.
The water flux was calculated based on the weight change of the permeate tank. The permeate conductivity was continuously monitored using a conductivity meter (VWR, Radnor, PA, USA). Each MD experiment was conducted using 800 ml of pretreated PW. It was assumed that pore wetting and membrane failure occurred once the permeate conductivity increased above 50 μS/cm. A regeneration cycle was conducted once the permeate conductivity reached 50 μS/cm or there was no weight increase of the permeate for 20 min. Regeneration of the membrane involved pumping DI water on both sides of the membrane at 0.5 L/min.
RESULT & DISCUSSION
A. EC Performance
During EC, the aluminium ions are generated continuously at the anode. The reduction of water takes place at the cathode, forming hydroxide ions. In the solution, a variety of aluminium hydroxides are produced when coagulating ions (aluminium and/or hydroxide ions) undergo hydrolysis in water. The reaction is the dominant reaction at pH 6.7, the pH of the PW. Introducing aluminium hydroxides can help destabilize suspended, emulsified and dissolved contaminants, which can further aggregate and precipitate as sludge or lift up to the surface as flocs. Soluble organic compounds can be adsorbed by the aggregated aluminium hydroxides. This adsorption phenomenon is a result of the liquid-solid intermolecular attraction forces between the adsorbable solute in the solution and the large surface area of the porous floc that forms.
The bipolar series (BPS) configuration was used in this work because only the first and last electrodes are connected to the power supply, simplifying the electrical connections. Further previous studies indicated that using BPS configuration can enhance the TOC removal. Initial experiments focused on determining an appropriate EC current and reaction time. A range of currents (1 to 9.5 A) and reaction times of 5 min and 20 min were studied. Each EC experiment was conducted using 600 mL of PW. After EC, the treated water was allowed to sediment for six h. Treated water was removed from the sludge and settled floc. Reaction that occur are as follow :
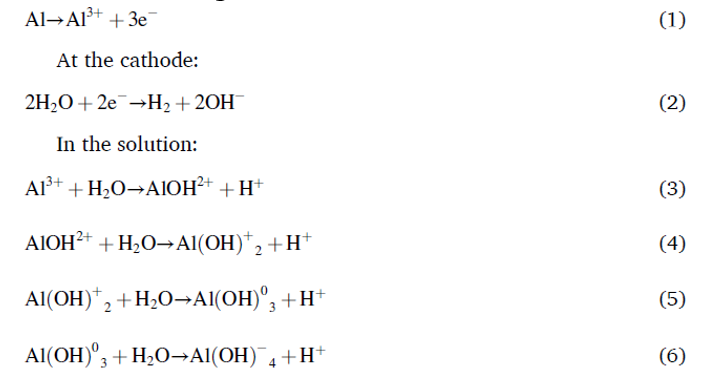
B. MF Performance
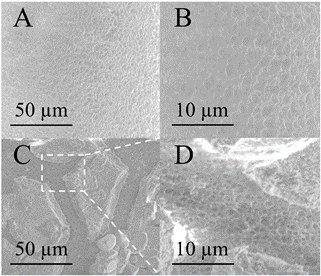
A digital photo of the MF membrane after filtration is shown in Fig. S1A, and the MF membrane after regeneration with DI water is shown in Fig. S1B. It can be seen that most of the flocs that had adhered to the membrane surface were removed after circulating DI water for one h. SEM images of the unused and regenerated MF membranes. Most of the regenerated membrane appears to have an open structure similar to the structure of the unused membrane. This suggests that regenerating the MF membrane by circulating DI water is sufficient to remove flocs from the membrane surface resulting in minimal irreversible fouling. There were tiny pieces of residual floc left on the regenerated membrane, which was observed by SEM. The gap between the flocs shows an open pore structure, which would have been occupied by the flocs before regeneration by DI water circulation. This further confirmed the pore structure was not irreversibly blocked by the flocs.
Particle floc size distribution was determined after EC for 20 min with an 8 A current using a Beckman Coulter (Indianapolis, IN) LS 13320 Laser Diffraction Particle Size Analyzer. The particle with a diameter larger than 0.1 μm contributed to 97.6% of the total sludge volume (based on the cumulative volume percentage). Although 31.5% of the particles have a diameter smaller than 0.1 μm based on the number percentage, they represent only 2.4% volume of the fouling layer on the surface of the MF membrane. In fact, a cake layer may be formed very quickly by large size particles. Thus, most of the smaller particles will be rejected by the cake layer through size exclusion. This can help prevent small particles from entering the membrane pores leading to irreversible pore blockage and fouling. The EDX result for the MF membrane indicates that fouling may be mainly caused by Al(OH)3, the major floc compound generated during EC.
C. MD Performance
The electrospun PVDF-HFP membrane behaved differently. Though the initial flux was similar to the commercial PVDF membrane, the flux dropped much more rapidly. In fact, the membrane had to be regenerated three times before the desired permeate volume of 250 ml was reached. As indicated in Figs. 10B, 11B and Table 5, for each subsequent run, though the initial permeate flux was similar, the rate of decrease of the flux was faster, and the volume of recovered permeate was less. However, the membrane could be regenerated, and the conductivity was always less than 50 μS cm 1.
In MD, the feed is typically kept at the same temperature in both the feed tank and the MD cell. However, as one approaches the solubility limit of the least soluble components in the feed, scale formation on the membrane is likely [38]. In fact, both concentration and thermal polarization will provide a driving force for precipitation on the membrane surface. In order to maximize the water recovery and membrane life, we would like to promote precipitation in the feed reservoir, not the membrane surface.
CONCLUSION
We have investigated a combined EC-MF-MD process for treating hydraulic fracturing PW. The PW investigated here had a TDS of 245,300 mg/L. Nevertheless, the process developed here could concentrate the rejection to the solubility limit of the dissolved salts. By reducing the temperature of the feed tank to 36 ◦C while the temperature of the feed entering the MD module was maintained at 60 ◦C, precipitation on the membrane is suppressed and occurs in the feed tank. We show that EC can lead to an adequate reduction in the PW TOC (67 mg/L), and MF can efficiently remove the particulate matter. The stability of the MD membrane is critical. Three different membranes with different surface properties were tested. An ideal membrane is one that provides high flux at high TDS and is resistant to breakthroughs. It is likely that the ideal membrane will depend on the TDS and other properties of the PW.
source : M. Jebur, et al. (2020). Combined Electrocoagulation-Microfiltration-Membrane Distillation for Treatment of Hydraulic Fracturing Produced Water. Elsevier
No Responses